6 Layer Rigid-flex PCB
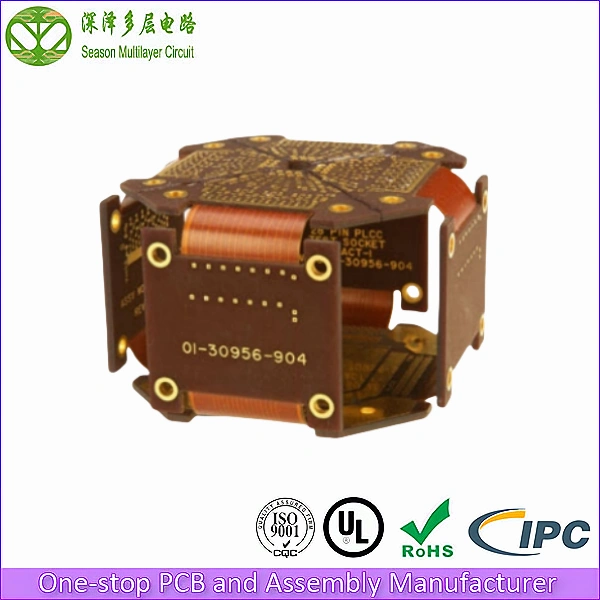
Rigid-flex PCB
Layer: 4L(Fr4)+2L(PI)
Material: Fr4+PI
Board Thickness: 0.15mm
Fr4 reinforcement: 0.2mm
Total Thickness: 0.35mm
Min Via Diameter: 0.2mm
Copper Thickness: 18μm
Trace Width/Spacing: 4/4mil
Surface Finish: ENIG1U”
6 layer rigid-flex pcb, using Shengyi FR4 substrate + Shengyi adhesive-less rolled copper PI. It is widely used in electronic devices, automotive electronics, medical instruments, medical equipment, industrial control, aerospace and other fields.
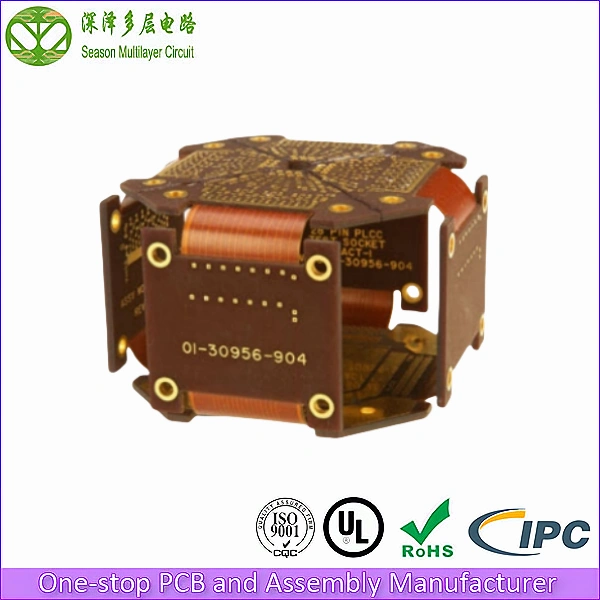
Innovative Rigid-Flex PCB Technology
Abstract
In the realm of electronic engineering, rigid-flex printed circuit boards (PCBs) represent a groundbreaking technological advancement that harmoniously combines the structural rigidity of hard substrates with the dynamic flexibility of soft materials. This white paper provides an in-depth examination of 6-layer (6L) rigid-flex PCB technology, detailing its conceptual framework, architectural composition, performance advantages, and diverse industrial applications. (Illustration below depicts one configuration of 6L rigid-flex PCB lamination structure)
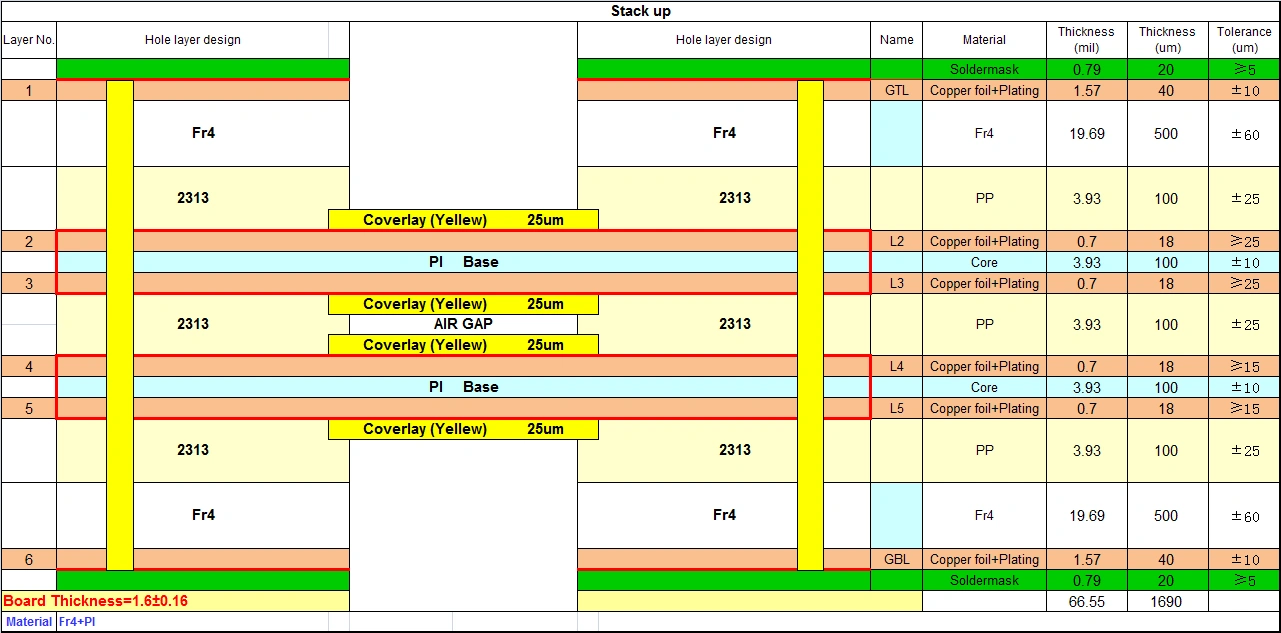
1. Conceptual Foundation of Rigid-Flex Technology
Rigid-flex PCBs constitute a hybrid composite material system that strategically integrates rigid substrates (typically FR4, ceramic, or fiberglass-reinforced epoxy) with flexible dielectric materials (primarily polyimide [PI] or polyethylene terephthalate [PET] films). This innovative material architecture has revolutionized modern electronic packaging, enabling unprecedented design flexibility in compact consumer electronics including smartphones, tablets, laptops, and wearable devices.
The evolutionary development of rigid-flex technology stems from the electronics industry’s persistent demand for:
- Miniaturization of component packaging
- Enhanced reliability in dynamic flexing applications
- Improved thermal and mechanical performance
- Reduction in interconnection complexity
2. Structural Architecture of 6-Layer Rigid-Flex PCBs
The 6L configuration represents an optimal balance between structural integrity and flexible performance, typically employing one of two fundamental stack-up configurations:
Configuration A: Symmetric Construction
- 2 rigid outer layers (top/bottom)
- 4 flexible inner layers
- Symmetrical copper weight distribution
Configuration B: Asymmetric Construction
- 4 rigid layers (top/bottom + 2 internal)
- 2 flexible transition layers
- Graduated impedance control
This sophisticated layering architecture delivers synergistic performance benefits:
- Rigid sections provide dimensional stability for component mounting
- Flexible zones enable dynamic bending (minimum bend radius ≥ 6x material thickness)
- Optimized thermal expansion coefficient matching
- Enhanced signal integrity through controlled impedance pathways
3. Performance Advantages and Technical Superiority
3.1 Impact Resistance
The viscoelastic properties of polyimide flex layers act as mechanical dampers, absorbing and dissipating impact energy through:
- Elastic deformation of polymer chains
- Microvoid compression in adhesive systems
- Distributed stress concentration points
Laboratory testing demonstrates 40-60% improvement in drop test performance compared to conventional rigid PCBs.
3.2 Fatigue Resistance
The 6L design achieves exceptional cyclic flex endurance through:
- Strain relief in neutral bend axis configuration
- Optimized copper grain structure (rolled annealed copper)
- PI film thickness gradients at bend transitions
Accelerated life testing shows >100,000 flex cycles at 90° deflection.
3.3 Structural Rigidity
High-performance rigid sections deliver:
- 0.5-1.5% elongation at break (FR4)
- 150-180°C continuous operating temperature
- 50-100N/mm² flexural strength
- <0.5% dimensional stability after thermal cycling
3.4 Manufacturing Process Maturity
Modern fabrication techniques ensure:
- ±25μm layer-to-layer registration
- Laser microvia drilling (50-100μm diameter)
- Plasma surface treatment for adhesion promotion
- Automated optical inspection (AOI) with <10ppm defect rates
4. Cutting-Edge Applications
4.1 Consumer Electronics
- Foldable smartphone hinge interconnects
- 360° laptop display cabling
- Wearable device conformal circuits
4.2 Automotive Systems
- Advanced driver assistance systems (ADAS)
- Heads-up display flexible interposers
- EV battery management system interconnects
4.3 Medical Technology
- Robotic surgical instrument arms
- Implantable neurostimulation leads
- MRI-compatible patient monitoring systems
4.4 Emerging Applications
- Aerospace: Deployable satellite antennas
- Industrial: Collaborative robot flex joints
- IoT: Structural health monitoring sensors
5. Future Development Trends
The next generation of 6L rigid-flex technology will incorporate:
- Embedded active/passive components
- Nanocomposite dielectric materials
- 3D printed conductive architectures
- AI-optimized flex circuit topologies
Conclusion
6-layer rigid-flex PCB technology represents the vanguard of electronic interconnection solutions, successfully merging the mechanical advantages of rigid substrates with the dynamic flexibility of soft materials. With its exceptional impact resistance, fatigue performance, structural stability, and manufacturing reliability, this technology continues to enable revolutionary advancements across multiple industries. As material science and fabrication techniques progress, 6L rigid-flex solutions will undoubtedly play an increasingly vital role in next-generation electronic systems.