Industrial PCBA
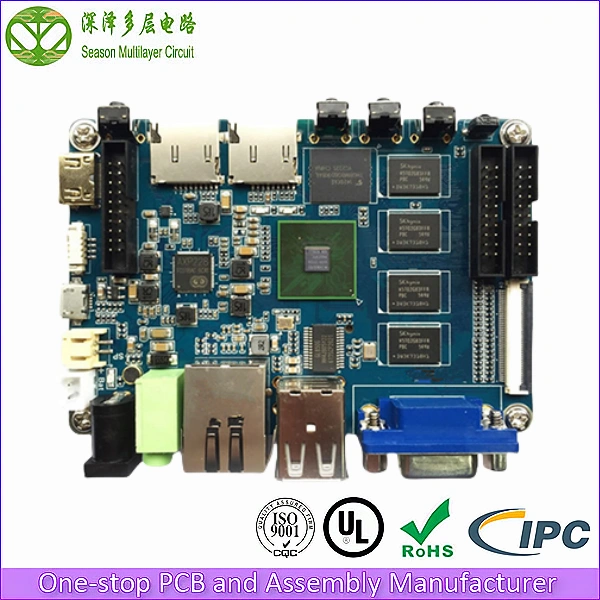
Industrial control PCBA
Material: Fr4 Tg150
Board Thickness: 1.6mm
Processing Size(Max): 510*460mm
Processing Size(Min): 50*30mm
Cell Size(Min): 0201
BGA Pitch: 0.35mm
BGA Diameter(Min): 0.18mm
Footprint: SOP、SOT、QFN、QFP、BGA
Industrial PCB – Designed for industrial control equipment computers, this type of product demands exceptionally high stability requirements
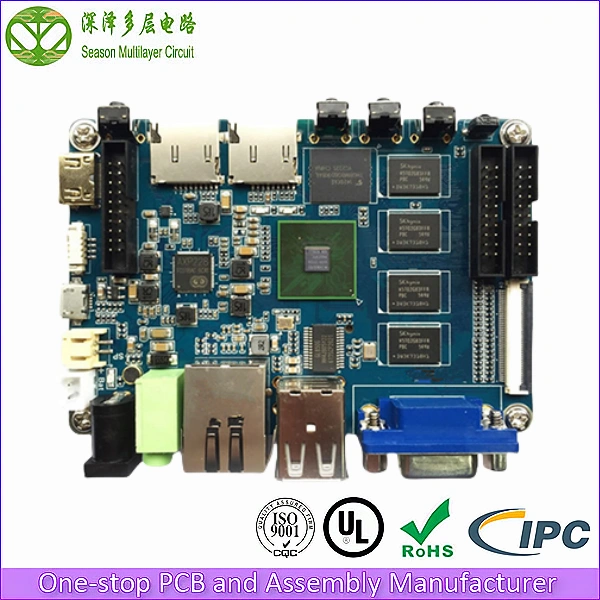
The Critical Role of Industrial PCBs in Modern Automation Systems
In the field of industrial control, Industrial Control Computers (IPCs) have become increasingly prevalent due to their high reliability and stability. These specialized computing systems ensure uninterrupted operation even in harsh environments, making them indispensable in industrial automation. At the heart of every IPC lies its Printed Circuit Board (PCB), a crucial component that significantly influences the performance and dependability of the entire system.
Understanding Industrial PCBs
An Industrial PCB is a printed circuit board designed to interconnect electronic components and circuits within an IPC. Unlike standard computer PCBs, industrial-grade PCBs demand superior design and manufacturing precision to withstand extreme conditions. Their complexity arises from the need to meet stringent environmental and operational requirements, ensuring long-term functionality in demanding industrial settings.
Key Requirements for Industrial PCBs
- Enhanced Reliability
Industrial control systems prioritize safety and stability, necessitating PCBs that can endure continuous operation under high workloads. Unlike consumer electronics, industrial PCBs must function flawlessly for extended periods without failure, minimizing downtime in critical processes. - Superior Electromagnetic Compatibility (EMC) and Anti-Interference Capabilities
Industrial environments are rife with electromagnetic interference (EMI) and mechanical vibrations. To maintain stability, industrial PCBs must incorporate shielding techniques, proper grounding, and optimized trace routing to mitigate signal distortion and noise. - Robust Thermal and Corrosion Resistance
Many industrial applications expose PCBs to extreme temperatures, humidity, and corrosive chemicals. High-quality materials with excellent thermal conductivity and protective coatings (e.g., gold plating or chemical nickel) are essential to prevent degradation and ensure longevity.
Design and Manufacturing Standards
To meet these rigorous demands, industrial PCBs must adhere to internationally recognized standards such as:
- IPC (Association Connecting Electronics Industries) guidelines for PCB fabrication and assembly.
- EIA (Electronic Industries Alliance) standards for component placement and signal integrity.
Design Considerations
- Optimized Layout & Routing: Careful component placement and signal path optimization reduce crosstalk and improve performance.
- EMC/EMS Testing: Electromagnetic compatibility (EMC) and electromagnetic susceptibility (EMS) tests validate the PCB’s resilience against interference.
- High-Density Interconnects (HDI): Advanced multilayer PCBs enable compact yet powerful designs for space-constrained applications.
Manufacturing Excellence
- Material Selection: High-performance substrates (e.g., FR-4, polyimide) with low dielectric loss and high thermal resistance are preferred.
- Precision Fabrication: Laser drilling, automated optical inspection (AOI), and controlled impedance manufacturing ensure defect-free production.
- Surface Finishes: Techniques like ENIG (Electroless Nickel Immersion Gold) and HASL (Hot Air Solder Leveling) enhance solderability and corrosion resistance.
Future Trends in Industrial PCBs
As Industry 4.0 and IoT-driven automation evolve, industrial PCBs must adapt to:
- Higher Processing Speeds: Supporting real-time data processing for smart factories.
- Miniaturization: Integrating more functionality into smaller form factors.
- AI & Edge Computing: Enabling predictive maintenance and autonomous decision-making.
Conclusion
Industrial PCBs are the backbone of modern automation, ensuring seamless operation in challenging environments. By adhering to stringent design protocols and leveraging cutting-edge manufacturing techniques, these PCBs deliver the reliability, durability, and performance required for next-generation industrial systems. As technology advances, continuous innovation in PCB engineering will remain pivotal in shaping the future of industrial automation.