Double Sided Medical FPC Proofing
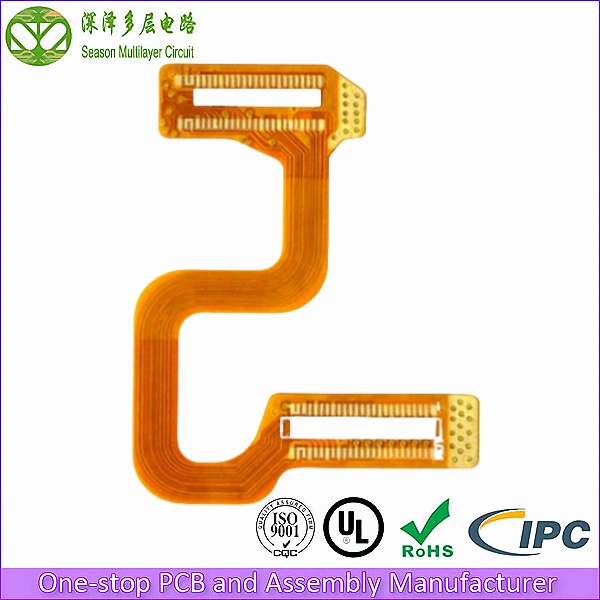
FPC Proofing
Layer: 2L
Material: PI
Board Thickness: 0.15mm
Fr4 reinforcement: 0.2mm
Total Thickness: 0.35mm
Min Via Diameter: 0.2mm
Copper Thickness: 18μm
Trace Width/Spacing: 4/4mil
Surface Finish: ENIG1U”
Double sided medical fpc proofing,the substrate material adopts Shengyi adhesive-coated rolled copper. The product is used for connectivity and signal transmission in medical electronic devices.
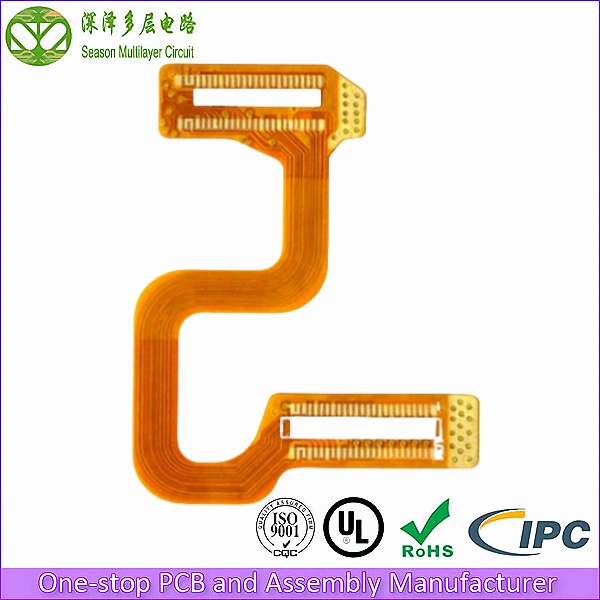
Revolutionizing Medical Devices: The Transformative Role of Double-Sided fpc proofing
In the rapidly evolving landscape of medical technology, double-sided flexible printed circuits (FPCs) have emerged as a groundbreaking innovation redefining device design paradigms. This advanced interconnect solution combines engineering excellence with clinical practicality, enabling medical equipment manufacturers to achieve unprecedented improvements in performance optimization, dimensional efficiency, and cost-effectiveness. This article provides a comprehensive analysis of double-sided medical FPCs, examining their technical specifications, operational advantages, clinical implementations, and transformative impact on next-generation medical systems.
Technical Fundamentals of Double-Sided Medical FPCs
Double-sided medical FPCs represent a sophisticated evolution in electronic interconnects, comprising three essential components:
- Flexible polyimide substrate with 12-50μm thickness range
- Dual-layer copper circuitry with 18-35μm copper foil
- Protective dielectric overlay (typically 25-75μm)
Unlike conventional single-layer FPCs constrained by planar circuit routing, this dual-layer architecture enables vertical interconnection access (VIA) technology implementation. The resulting three-dimensional circuit configuration achieves 2.8-3.5 times greater wiring density compared to single-sided alternatives, with typical line width/spacing specifications reaching 50/50μm in advanced implementations.
Performance Advantages in Medical Applications
- Enhanced Signal Integrity
The multilayer architecture minimizes electromagnetic interference (EMI) through optimized ground plane configuration, achieving 40-60dB improvement in signal-to-noise ratio (SNR). This proves critical in high-frequency medical applications such as MRI gradient coil control (operating at 50-200MHz) and ultrasound transducer arrays requiring <0.1% signal distortion. - Space Optimization
Medical-grade double-sided FPCs achieve component density of 120-150/cm² compared to 40-60/cm² in single-layer counterparts. This spatial efficiency enables 60-70% size reduction in implantable devices like next-generation neurostimulators (now <3cm³ volume) while maintaining full diagnostic capabilities. - Economic Viability
Advanced roll-to-roll manufacturing processes reduce material waste by 35-40%, translating to 20-25% cost savings over conventional FPC production. The simplified lamination process (3-step vs. 5-step in single-sided) further enhances production scalability for high-volume medical applications.
Clinical Implementation Scenarios
- Medical Imaging Systems
In CT scanner gantry applications, double-sided FPCs enable 1024-channel data transmission with <1ns signal skew across 2m rotating interfaces. For 3T MRI systems, they achieve 400MHz analog signal transmission with <3° phase variance, critical for high-resolution diffusion-weighted imaging. - Implantable Medical Devices
Cardiac rhythm management devices now utilize biocompatible FPCs with:
- 0.1mm bend radius durability for 10-year implantation
- 500kΩ+ insulation resistance in physiological saline
- 0.5g/m² ion release rates meeting ISO 10993 standards
- Portable Diagnostic Equipment
Handheld ultrasound probes employing double-sided FPCs demonstrate:
- 15μm thickness conforming to 5mm probe diameter
- 200Vpp voltage handling for piezoelectric excitation
- 85°C operational stability during sterilization cycles
Performance Enhancement Mechanisms
- High-Speed Data Transmission
The differential pair routing capability supports 25Gbps data rates in digital X-ray detectors, reducing image reconstruction time by 40-60% compared to conventional cabling solutions. - Enhanced Reliability
Accelerated life testing shows 98.7% survival rate after 50,000 flex cycles (IEC 60601-2-52 compliant), crucial for robotic surgical instruments requiring precise movement reproducibility. - Thermal Management
The 0.8-1.2W/m·K thermal conductivity facilitates efficient heat dissipation in RF ablation catheters, maintaining tissue contact surfaces below 45°C during prolonged procedures.
Future Development Trajectory
Emerging innovations include:
- Stretchable FPCs with 200% elongation capacity for wearable biosensors
- Bioresorbable substrates for temporary implant monitoring
- 8-layer HDI FPCs integrating wireless modules in capsule endoscopy
Industry projections indicate 18.7% CAGR growth for medical FPC proofing through 2030, driven by increasing demand for minimally invasive surgical technologies and AI-enhanced diagnostic systems.